A team of University of Regina engineering graduates has combined high tech—artificial intelligence, GPS, and big data—with social marketing to solve a “wicked” waste problem: recycled materials that end up in landfill. Photo by Kiriako Iatridis
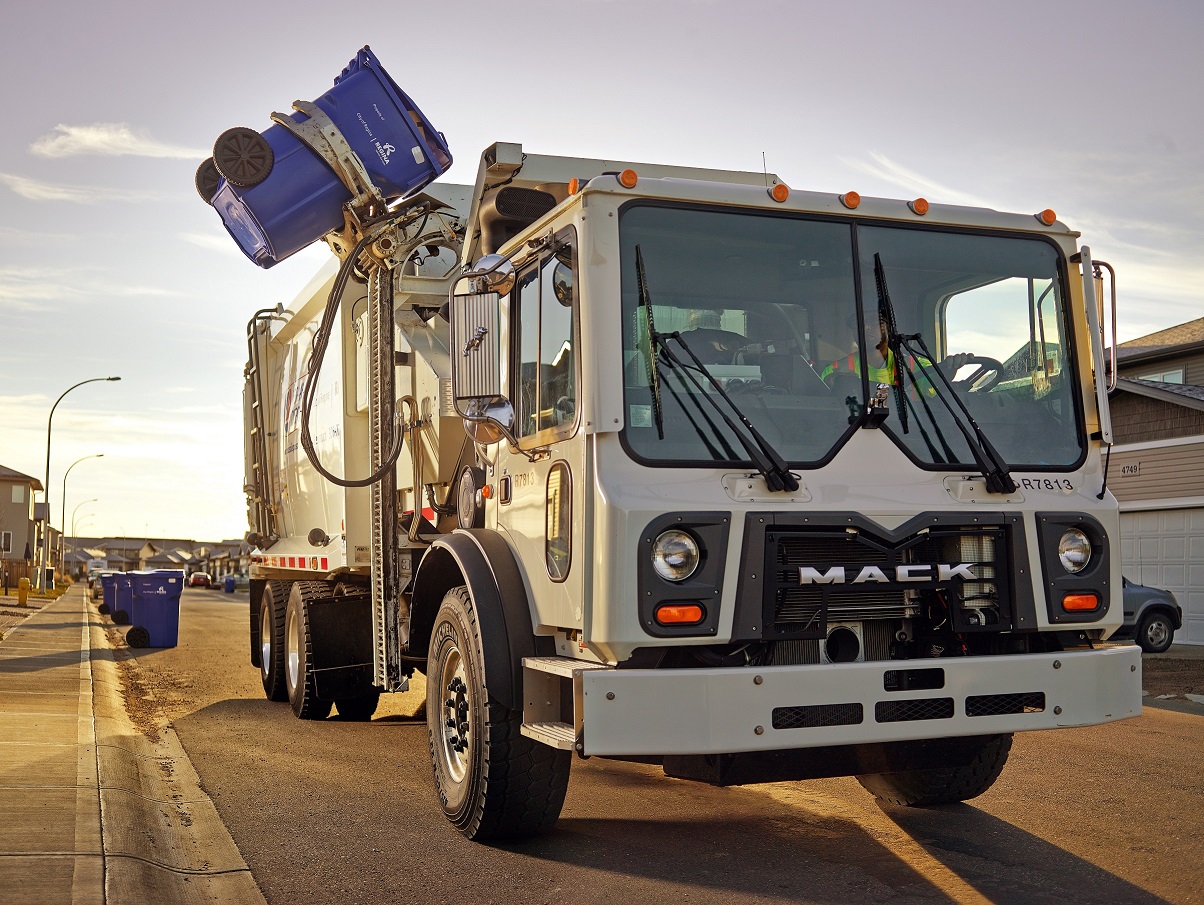
A team of University of Regina engineering graduates has combined high tech—artificial intelligence, GPS, and big data—with social marketing to solve a “wicked” waste problem: recycled materials that end up in landfill.
“Reduce, Reuse, Recycle.” It was an early mantra of the environmental movement, coined after the first Earth Day in 1970. While consumer society was reluctant to “reduce” and too busy to “reuse,” distaste for conspicuous waste fuelled an appetite to “recycle”.
Segregating plastics and glass from paper and metal was complex enough, but too often the recycling stream was also contaminated during collection.
Recycling emerged as one concrete way people could to do something about the environment. Public pressure to set up recycling systems became intense. That, and the monumental cost of building new landfill sites, led to the adoption of curbside recycling as a favoured waste management solution across Canada and around the world.
Participation was robust, yet concerns about the inadequacies of recycling programs undermined public confidence. It was rumoured that a lot of material dutifully put in the blue bin is not actually recycled. There was some truth to these rumours: A limited and fickle market for recycled products was part of the problem; contamination was another.

Segregating plastics and glass from paper and metal was complex enough, but too often the recycling stream was also contaminated during collection. Contaminants included both items that simply aren’t recyclable and, more problematic, things like motor oil, wet kitchen waste, even diapers, which leak onto other materials in the collection truck, making them impossible to recycle. Recycling workers who sorted material were at risk due to unsanitary and dangerous items, including used needles. Consequently, up to a third of recycled material could end up in landfill.

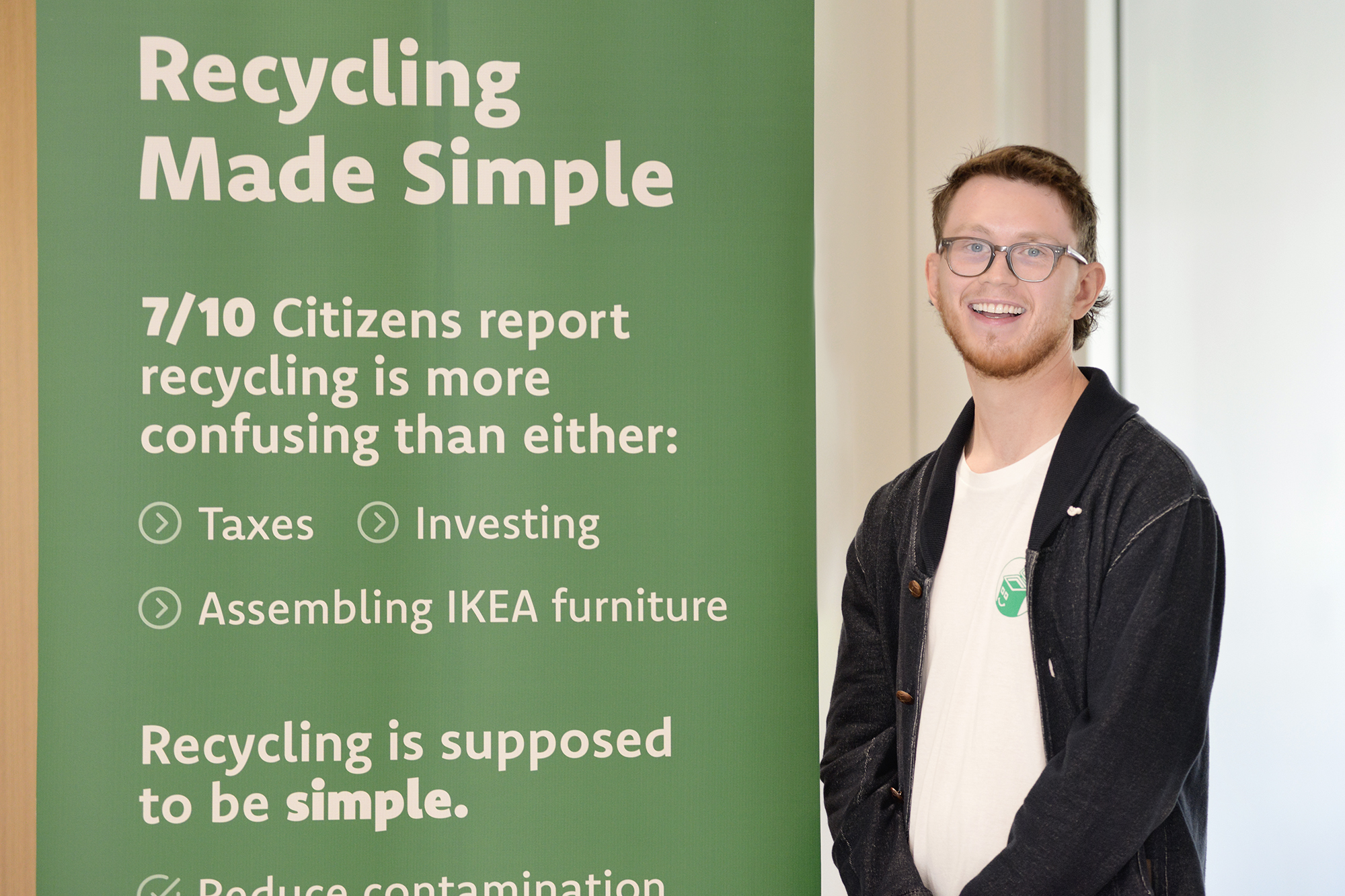
Enter Prairie Robotics and the company’s co-founder and CEO, Sam Dietrich BASc'17 . The University of Regina engineering grad envisioned a high tech solution to contaminated recyclables: use smart technologies to solve the problem.
Along with cofounder and Chief Technology Officer (CTO) Stevan Mikha BASc'16, another U of R engineering grad, Deitrich formed Prairie Robotics.
“Our first product,” says Dietrich, “was an artificial intelligence (AI) application to support self-driving tractors. It was sold to DOT Technology Corp and ultimately landed with farm equipment manufacturer Case-New Holland, which has commercialized the technology.”
Looking for new opportunities, Dietrich and Mikha responded to Innovation Saskatchewan’s “Innovation Challenge.” Launched in 2017, Innovation Challenge was designed to generate novel solutions to public sector challenges by harnessing ideas from made-in-Saskatchewan start-up technology. The program aimed to benefit innovators by co-developing solutions that result in commercial opportunities, applying innovations to real-life settings, and enabling companies to receive feedback from large customers.
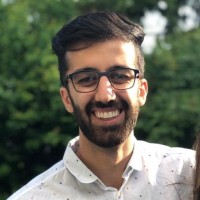
One solution Saskatchewan’s Ministry of Environment was asking for was a way to measure the content of the waste stream at landfill sites. Prairie Robotics submitted the successful proposal, called SightScale, which opened a door to Saskatchewan’s “innovation ecosystem.”
Dealing with waste is a “wicked” environmental problem, i.e. it’s highly complex and extremely difficult to solve. Recycling seems like an obvious solution, but technical, economic, and social factors limit its efficacy. Contamination is one of those factors.
How big a problem is it? Consider the experience of one of Saskatchewan’s largest waste management companies, Saskatoon-based, Loraas Recycle.
Loraas Recycle collects an average of 25,000 tons of recycling annually. The contamination rate is 20 percent on average, but Loraas has seen loads with contamination as high as 55 percent. In this case, “contaminant” means things that are simply not accepted in the recycling stream, things like wood or bricks.
Loraas Recycle also estimates that 15 percent of acceptable recyclables have been ruined by coming into contact with things like organic waste or diapers. In fact, if all the diapers that go through the Loraas system in one year were laid out in a line it would be 140 km long!
In all, some 35 percent of the material Loraas Recycle collects has to be redirected to the landfill. In addition to the environmental impact, it is a costly problem for waste management companies and municipalities alike.
Separating and redirecting contaminants to the Loraas landfill costs $500,000 to $875,000 annually, just for landfill tipping fees. Trucking the material—six 30-yard bins a day—also results in increased costs and adds to the company’s carbon footprint.
Contaminants also impact the machines used to sort materials and can even shut down the system. A fire caused by a lithium battery closed the Loraas facility for eight weeks in 2018.
Contaminants can also endanger employees. The presence of sharp objects, for instance, has led to workplace injuries. Loraas Recycle reports that it removes eight 5-gallon pails of needles from the recycling stream in a typical year.
Working directly with the people in the recycling business at the Regina landfill was an eye opener for Prairie Robotics. Listening carefully to their observations, Dietrich and Mihka came to understand that, rather than measuring the problem at the landfill, what was really needed was a way to identify and prevent contamination at source—the recycling bin behind every household.
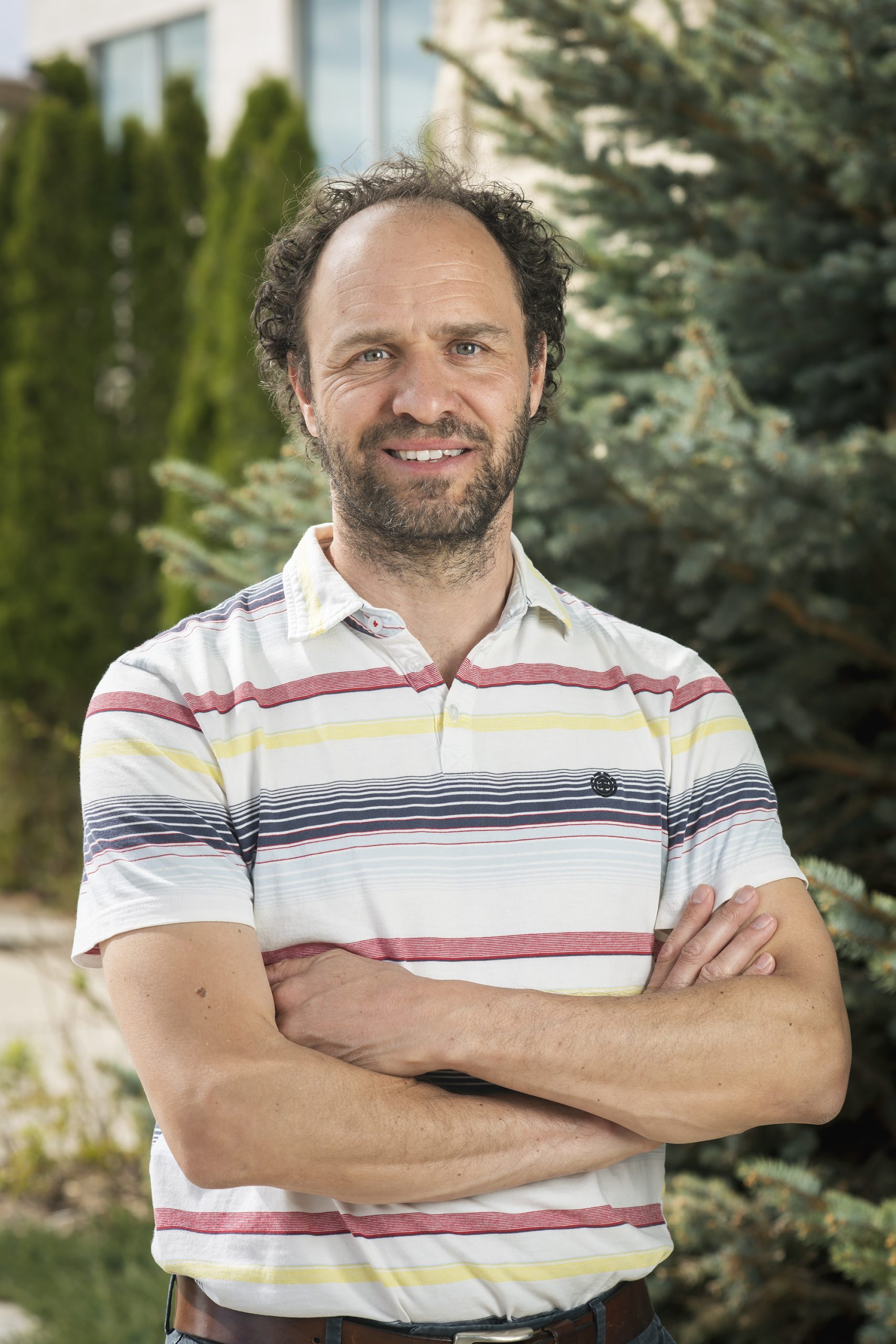
“Sam and Stevan were adept at listening to stakeholders,” says Andrew Wahba, Director at Innovation Saskatchewan. “They did a great job of going after the opportunity that actually existed as opposed to what they were initially aiming for. Pivoting like that is an critical skill for a start-up business.”
They also learned that a key factor underlying the problem was public education. Most people want to recycle, but many are confused by what can and cannot be tossed into the blue bin. In general, people won’t research this themselves, but they do respond to direct feedback.
For the City of Regina and an a number of other locales, what had proven effective in reducing contamination at source was sending staff out to check recycling bins and then making direct contact with homeowners who put undesirables in their bin.
Regina provides bi-weekly recycling collection to over 65,000 households, collecting over 7,000 tonnes of recyclables annually. Contamination impacts the income from and the costs of recycling programs. Being able to increase revenue and decrease costs was a motivating factor in 2019 when City staff undertook 6,000 recycling audits at 2,000 Regina households. This made it possible to provide people with direct feedback about common sorting mistakes. Of the carts audited, 73% were contaminated on the first visit. After receiving initial feedback, over 70% of households had improved their recycling habits by the second visit.
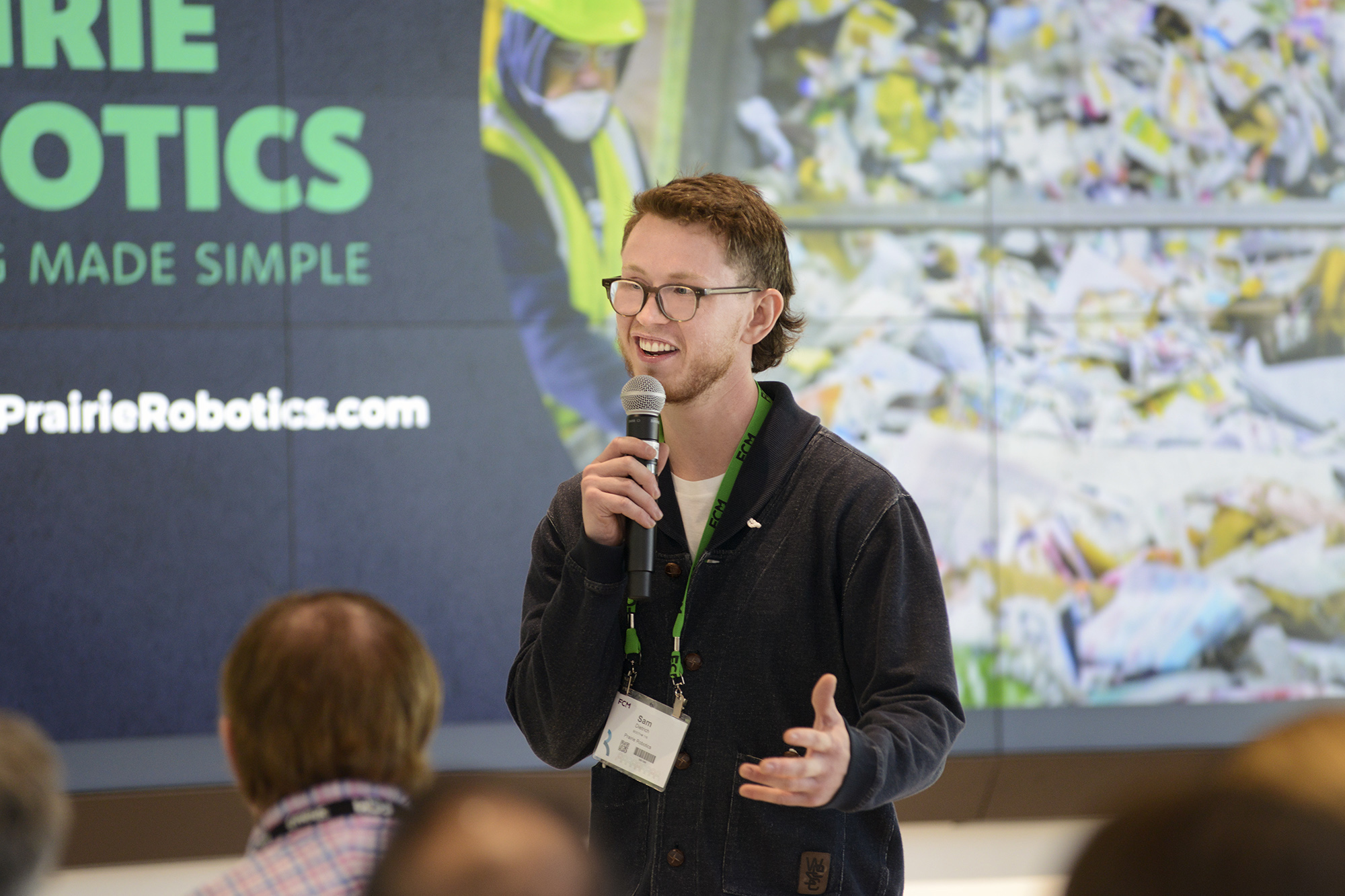
This approach was effective, but checking 65,000 bins was formidable. Having seen the success of targeted education, the City was looking to expand the program. Working with Prairie Robotics to leverage the power of automated audits looked promising.
The Prairie Robotics team succeeded in assembling a suite of technologies to automate the job. In a nutshell, here’s how it works. A camera mounted on a recycling truck records images of the contents of blue bins as they are dumped into the truck’s hopper. The location of each bin is tracked using the Global Positioning System (GPS). AI is then used to examine images of the contents to check against an inventory of various known contaminants. The data can then be used to identify which contaminants have been deposited at a specific household. When a problem is identified, the system automatically generates a postcard or email, which includes an image of the contaminant. It is sent to the household as a friendly reminder that the item can’t be recycled and should be put in the trash bin.
“You begin by collecting hundreds of thousands of images, using different lighting and poses,” says Dietrich, “and labelling the contaminants you are interested in. Essentially, you are training artificial intelligence to sort through thousands of new images to identify contaminants.
“Initially, we identified thirteen important contaminants but we continue to add more. Some that are more difficult to catch are hazardous items that quite rare, such as needles, batteries, or even propane tanks.”
Speaking of the role of his training at University of Regina, Dietrich says, “I have a degree in applied science in industrial systems engineering, with a double minor in electronics and software systems engineering. Obviously that’s the right background for what I’m doing. But the part of my education that I actually use the most today is not so much related to specific software, it’s more how to identify the problem. ‘A problem well defined is half solved,’ as they say.
“Actually, eight of ten staff at Prairie Robotics are University of Regina students,” says Dietrich. “Our CTO, Stevan Mikha, did his degree in electronic systems engineering. He is currently completing a Masters program focused on machine learning for network penetration. He has become adept at explaining our technology to clients.”
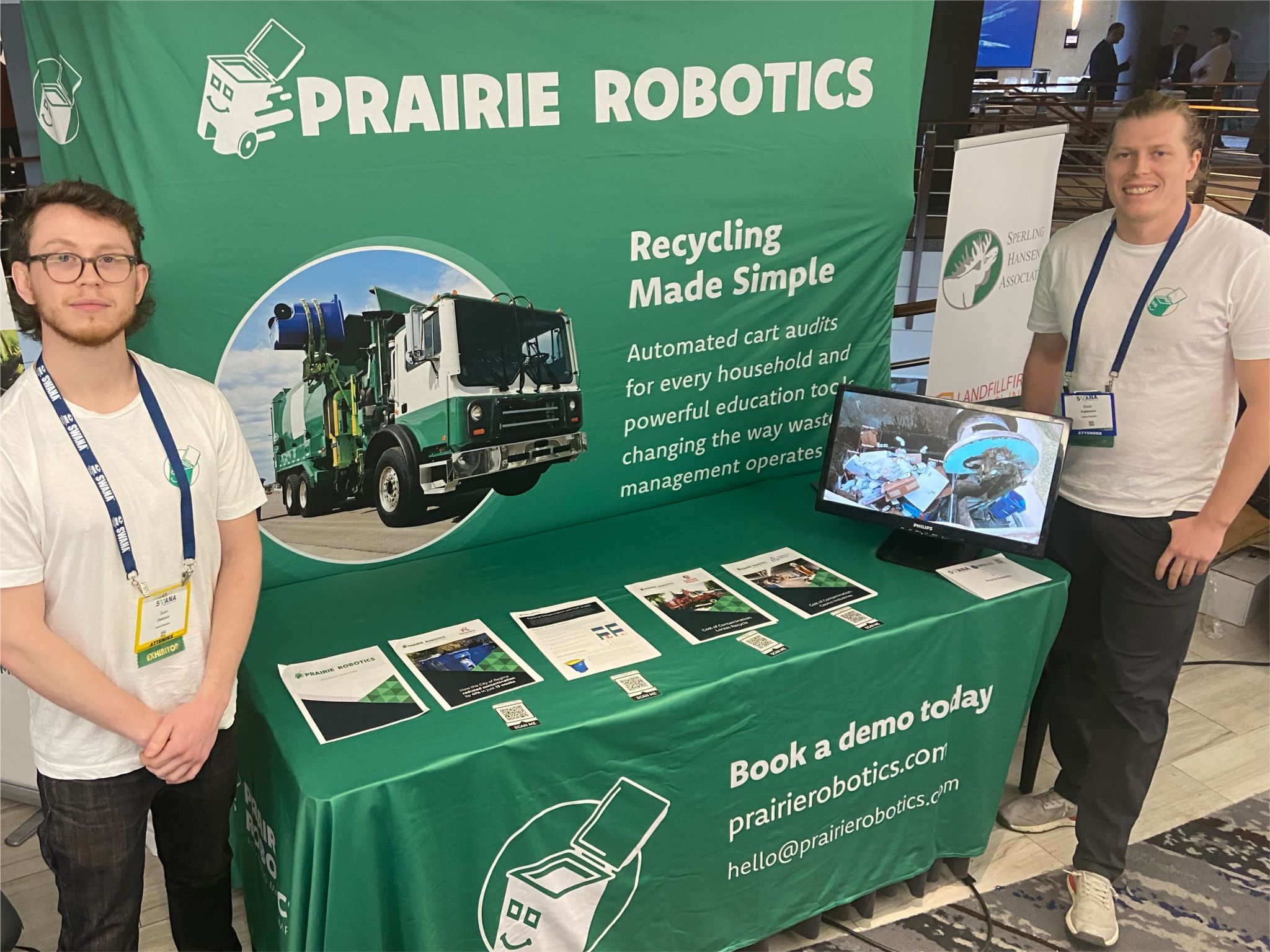
For a tech start-up, a bright idea is only half the battle. A next step is proof of concept. Prairie Robotics was able to set up a pilot project in collaboration with the City of Regina to test the approach in a neighbourhood. An initial four-month trial period was used to benchmark the technology.
“Our technology was installed on one collection truck,” reports Dietrich. “The first month was used to establish a baseline for performance: what was the current level of contaminants in the bins. Over the next three months, bin contents were analyzed using AI and educational postcards were sent to households when contaminants were detected. The postcard described the importance of proper recycling and included a picture of the specific household’s previous collection with contaminants highlighted and other items blurred from view.”
The automated system performed over 40,000 audits (an 8-fold increase over the manual program) and generated over 10,000 postcards. The pilot was a success, with over 70 percent of 11,875 households improving their recycling practices after their first audit, with continued improvement over subsequent weeks. Total contamination decreased by 41.5 percent. The cost of the pilot was $21,900, including public education.
The Prairie Robotics platform is capable of outperforming manual audits in both volume and consistency, resulting in greater impact for municipalities. And more that 99 percent of all postcards were received without compliant.
With a successful pilot under its belt, Prairie Robotics was ready to engage with a number of government and industry support programs and ultimately to attract investors. One important step was working with a program called Cultivator, Regina’s first start-up incubator and Canada’s first credit union-led incubator. Sponsored by Conexus Credit Union, its objective is to launch, grow, and scale innovative Saskatchewan tech companies.
“Cultivator included training on business, marketing, product feedback, growing a team—it was a boot camp for starting and running a business,” says Dietrich. “It also included a pitch competition, which we were fortunate to win, adding another $10k to our capital.
“Each step of the way we have had a lot of support from the Regina and Saskatchewan business communities. The City of Regina was our first commercial client and we also had an opportunity to work with Loraas Disposal, Saskatchewan’s largest waste and recycling service provider.”
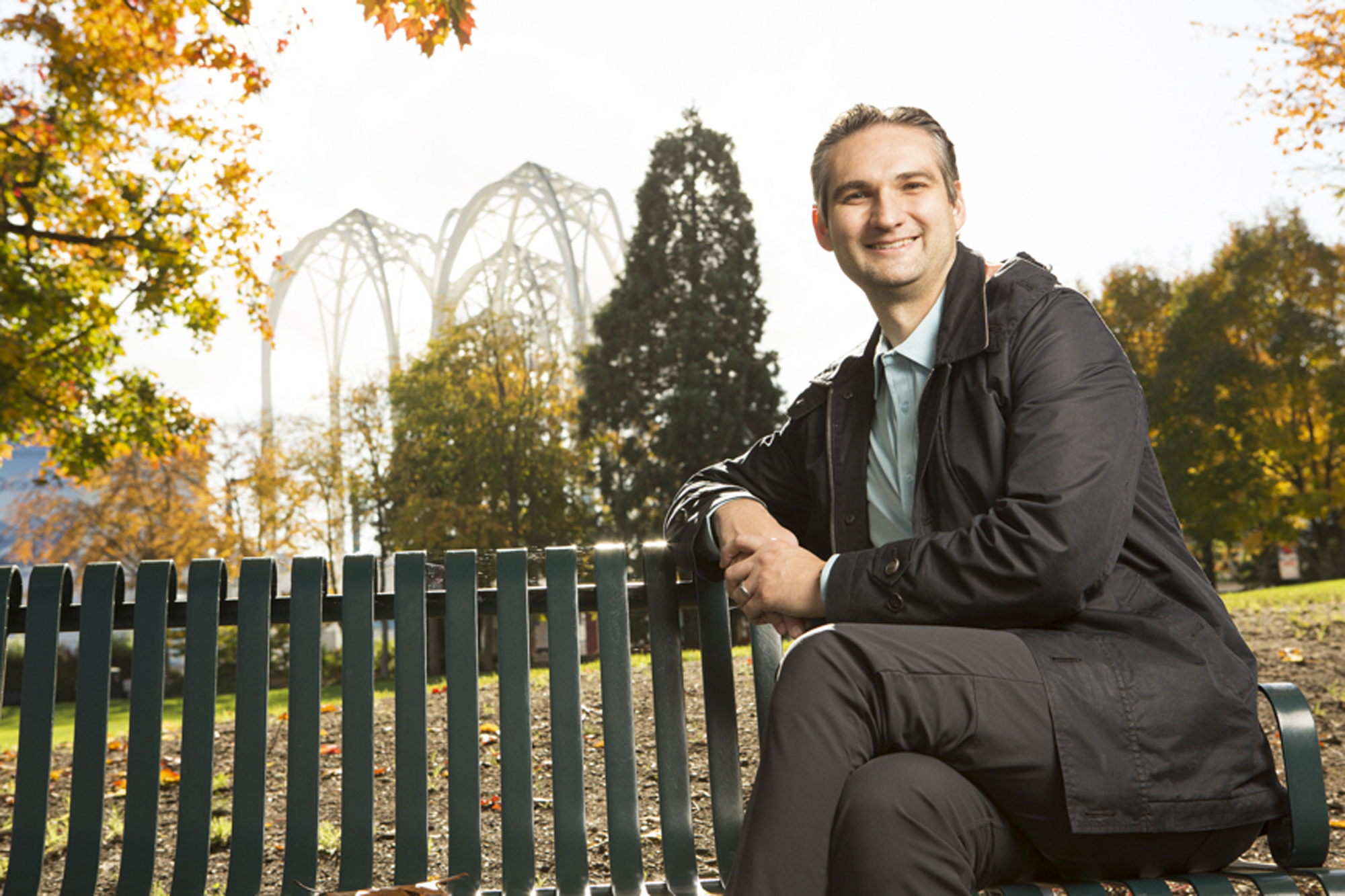
Support also came from Co.Labs, an independent not-for-profit resource for tech start-ups. The Saskatchewan Advantage Innovation Fund (SAIF) helped with commercialization, and the Saskatchewan Technology Startup Incentive (STSI) acted as major motivation for investors. In addition, Prairie Robotics was one of 30 companies (and the only Saskatchewan company) admitted to Canada’s top AI accelerator, Next AI, a program to boost artificial intelligence-based ventures and commercialization.
“We were also provided introductions to several investors, including entrepreneur Kerry Lumbard; Dan Cugnet, former owner-operator of Goliath Disposal; and Max Schmeiser BA'03, VP, Studio and Content Data Science & Engineering at Netflix, who is from Regina. They are all committed to giving back to Saskatchewan. Their support was instrumental in raising $690k in seed funding to build our business.”
Andrew Wahba notes that, “Sam is very effective at ‘creating his own luck’. He seeks out the innovation ecosystem, looking at all the programs and supports out there, across the province and country. He’s really strong at using that programing to take his company to the next level. I am excited to see where they are at and where they are going.”
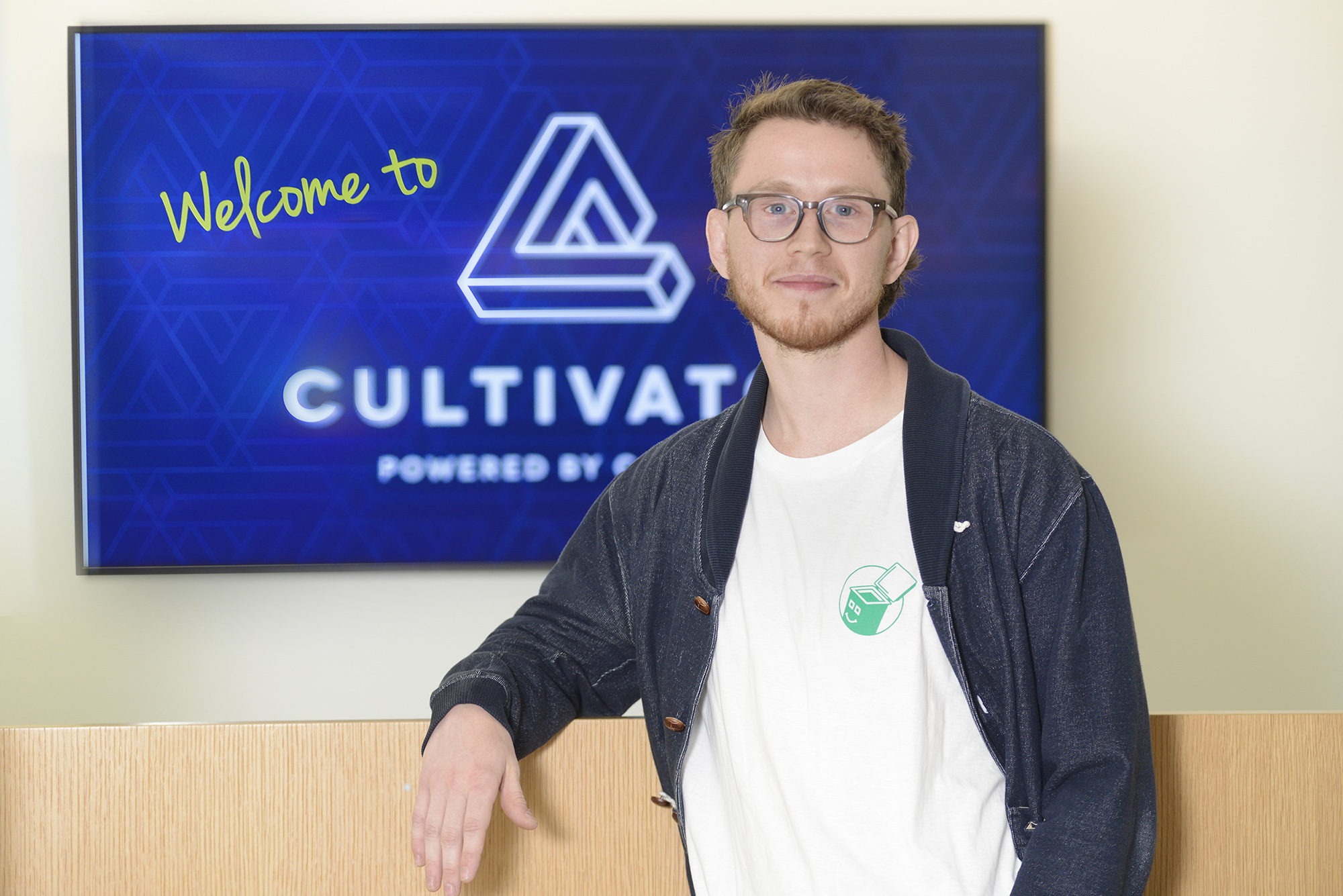
The potential market for technology that can improve the success of recycling systems is huge: essentially, every municipality and waste management company could benefit. Currently, Prairie Robotics is collaborating on projects with a number of western Canadian municipalities, with expansion to the United States in sight.
To track the progress of Prairie Robotics, visit their website at www.prairierobotics.com.